Six Sigma is a data-driven methodology aimed at improving business processes by reducing defects and variability. Originating from manufacturing, it now applies across industries such as healthcare, finance, and IT. Its ultimate goal is to enhance operational efficiency, customer satisfaction, and profitability by implementing a disciplined, data-driven approach to eliminate process inefficiencies.
Six Sigma combines quality management tools, statistical analysis, and project management methodologies. Businesses that adopt Six Sigma strive for nearly flawless operations, reducing costs, increasing productivity, and improving customer experiences.
Core Philosophy of Six Sigma
Six Sigma is built on the philosophy of continuous improvement. Its foundation lies in two key principles:
- Reducing Variation: Minimizing inconsistencies in processes to ensure predictable and reliable outcomes.
- Enhancing Quality: Striving for near-perfect products or services by achieving minimal defects.
The name “Six Sigma” signifies a statistical standard of quality that allows for only 3.4 defects per million opportunities (DPMO), setting a high benchmark for operational excellence.
Six Sigma’s principles are supported by a range of tools and methods, including statistical process control, root cause analysis, and project management frameworks. This systematic approach ensures that every aspect of a business process is optimized for performance and quality.
The 6 Steps (DMAIC)
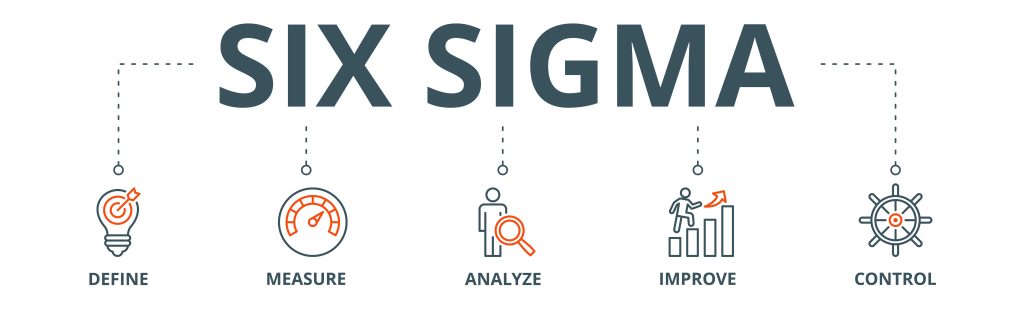
The Six Sigma process follows the DMAIC framework, a structured approach to problem-solving:
- Define: Identify the problem, set goals, and outline project scope. This step involves understanding customer requirements and setting clear objectives.
- Measure: Collect relevant data and establish current performance baselines. Measurement ensures that the process’s starting point is well understood.
- Analyze: Investigate root causes of process inefficiencies. This involves using data analysis techniques like fishbone diagrams, Pareto charts, and regression analysis.
- Improve: Develop and implement solutions to address identified issues. Improvement efforts might include redesigning workflows, automating repetitive tasks, or training employees.
- Control: Monitor results to maintain improvements over time. Control measures include establishing standard operating procedures and ongoing process audits.
- Sustain: Ensure long-term success through continuous evaluation. Businesses must create a culture of ongoing improvement by encouraging feedback and monitoring metrics regularly.
What Does the Six Sigma Level Mean?
Reaching the Six Sigma level means achieving nearly perfect process performance. Statistically, it equates to a process operating with a defect rate of only 3.4 DPMO, indicating world-class quality. Organizations operating at this level enjoy reduced costs, improved customer satisfaction, and a stronger competitive edge.
Achieving Six Sigma requires an unwavering focus on data, performance measurement, and strategic project implementation. It also involves developing a team of certified professionals to lead and support improvement initiatives.
How It Works
Six Sigma works by utilizing statistical tools and techniques to analyze and improve business processes. Teams of certified professionals, often called Black Belts, Green Belts, and Master Black Belts, lead projects focused on eliminating waste, reducing process variation, and boosting overall efficiency.
Six Sigma projects are often driven by specific business goals, such as improving production yields, reducing cycle times, or enhancing service quality. Project teams follow a structured roadmap, applying data-driven insights to implement lasting improvements.
Six Sigma Examples in Real-World Applications
- Manufacturing: Reducing production defects in automotive assembly lines, ensuring quality and reducing costs.
- Healthcare: Improving patient care, reducing medical errors, and decreasing wait times in hospitals and clinics.
- Finance: Streamlining loan approval processes, enhancing customer service, and minimizing credit risks in banking institutions.
- Supply Chain Management: Optimizing logistics and reducing shipping delays.
- Customer Service: Enhancing customer support processes through faster response times and more accurate issue resolution.
Six Sigma vs. Other Methodologies
Aspect | Six Sigma | Lean Management | Total Quality Management (TQM) |
---|---|---|---|
Focus | Quality improvement | Waste reduction | Comprehensive quality focus |
Approach | Data-driven | Process-driven | Management philosophy |
Key Tools | Statistical tools | Value stream maps | Continuous improvement plans |
Six Sigma complements other methodologies like Lean Management and TQM, offering a comprehensive framework for achieving operational excellence by focusing on data-driven problem-solving.
Steps to Certification
- White Belt: Basic understanding of Six Sigma principles, terminology, and core concepts.
- Yellow Belt: Active participation in improvement projects, supporting Green and Black Belts.
- Green Belt: Managing smaller projects under Black Belt supervision, applying statistical tools, and leading process improvements.
- Black Belt: Leading complex projects, mentoring team members, and driving organization-wide improvements.
- Master Black Belt: Strategic role involving Six Sigma program management, policy development, and executive-level leadership.
Certification typically requires completing a training program, passing a certification exam, and successfully managing Six Sigma projects.
Tools & Software for Six Sigma
- Statistical Analysis Tools: Minitab, Excel, JMP, and SAS.
- Project Management Tools: Microsoft Project, Trello, Asana, and SystemX
- Data Visualization Tools: Tableau, Power BI, and QlikView.
- Process Mapping Tools: Lucidchart, Visio, and Bizagi.
- Workflow Automation Tools: Automation Anywhere, UiPath, and Blue Prism.
Challenges in Implementing Six Sigma
- Cultural Resistance: Employees may resist changes to established processes.
- Training Costs: Certification and training can be expensive, especially for large teams.
- Data-Driven Demands: Successful projects rely on accurate data collection and analysis.
- Management Commitment: Sustained leadership support is crucial for long-term success.
- Resource Allocation: Allocating time and resources while balancing operational needs can be challenging.
Future Trends in Six Sigma
- Integration with AI & Automation: Leveraging artificial intelligence for smarter process analysis and predictive modeling.
- Digital Transformation: Applying Six Sigma to digital process improvement, especially in IT and software development.
- Sustainability Projects: Using Six Sigma to support eco-friendly business initiatives and sustainability goals.
- Industry-Specific Adaptation: Tailoring Six Sigma for emerging industries like renewable energy, fintech, and healthcare tech.
By mastering Six Sigma principles, businesses can unlock new levels of efficiency, reduce operational costs, and boost customer satisfaction. Start your journey toward process excellence today!